1. What sort of client is looking for a prefab project?
In our project’s case, the client actually led the prefab idea. The clients were well-educated about the process and saw it as a way to build affordably given a situation they hadn’t expected facing. This affordability sometimes comes from a reduced construction cost (I’ll talk about this more later), but more reliably comes from a reduction in construction time. This reduces the amount of time that the homeowner must cover the mortgages, taxes, and upkeep for both their current and new properties. There are many times when the idea of prefab won’t even be on the client’s radar; in this case it is the contractor or architect’s turn to introduce it if it’s appropriate.
2. What situation lends itself to prefab?
The client’s situation also drove the prefab decision. They are a three-generation family who wanted good schools within easy reach of Philadelphia. Both parents work in the city, and the grandmother takes care of the children during the day. Houses in the clients’ chosen school district are large, but most were either too expensive or needed too much renovation to make them work. They did, in fact, find an existing house that met many of their needs. However, some extenuating circumstances led to the desire to do a more extensive remodel where incorporating modular construction made more sense, for several reasons.
The factory-built modules would be of very high quality, meaning that the new structure would be just as solidly built as its neighbors. And the reduced on-site build time meant less noise and traffic pollution for everyone, including the nearby elementary school. In fact, the main bulk of the house was erected in just six days. Finally, by starting with a pre-designed floor plan, the clients could save time and money on design.
Inside the factory.
3. What are the possibilities, limitations, and benefits?
Many people think of prefab as just Dwell-magazine modern. However, there is no limitation to the possible styles. In this case, the clients wanted (and got) a Tudor-style home. You can visit the websites of many manufacturers to see what they offer, and remember that many of them will do custom work.
As far as floor plans go, the sky’s the limit. This home was closely based on a stock plan from the manufacturer, but small tweaks were made. In particular, this house needed to connect to the remaining portion of the previous house–a small stone building that was likely the first home on this property–via a breezeway from the breakfast nook. The main limitation is the size of the modular boxes. They are limited, of course, by the highway. The largest units are typically 16′ x 45′.
In the existing house, the old stone building was buried within many additions.
Now, the original stone portion is exposed and is connected to the new prefab home by a site-built breezeway.
The benefits of prefab are numerous. The majority of the building is constructed under climate-controlled factory conditions. This means that the interior is never exposed to rain, a source of squeaks and, sometimes, mold. The modules are very sturdy, since they have to survive a road trip. Because the whole thing is built inside, there are no work delays due to weather.
From a green standpoint, the number of worker miles driven is greatly reduced over the course of the project. Factories also tend to be built where they have easy access to materials, so large quantities can be delivered to the factory over shorter distances, thereby reducing those miles. Module sizes are optimized to reduce cutoff waste, and scraps are saved and used as needed on future projects.
The cost savings for prefab are hotly debated. Some claim that a stock plan modular house will cost 10%-15% less than its site-built comparison. Others say it actually costs more, given the inevitable upgrades, tweaks, and additions. However, when it comes to schedule there is no comparison. The ability to construct the modules concurrently with the demolition, site preparation, and foundation construction greatly reduces the overall project schedule. The optimized, assembly-line style factory process is also a contributing factor to time savings.
4. Who are the team members?
For this project, the main team members were the modular company (Simplex), the homeowners, the local general contractor (Orion GC), the site engineer, the structural engineer, and the architect (me, of course).
The modular company provided the initial house design and its foundation requirements. They were responsible for specifying all the materials to be used in the house, and of course for manufacturing it. They delivered the “boxes” and set them in place.
Setting the fifth module of the main house.
It was the site engineer who first alerted the client to the idea of marrying a portion of the existing building with the new, which made the site requirements much easier to deal with. This engineer also helped manage much of the permitting process with the Township.
My initial role was to help determine which parts of the existing house could be saved and how they could be integrated into the new house, which was based on a pre-designed prefab floor plan. As the project progressed, I became more involved in tweaking the prefab design to meet the clients’ needs. I also designed the links between the old and new portions and between the house and the garage, and documented the basement and foundations. The structural engineer assisted as needed.
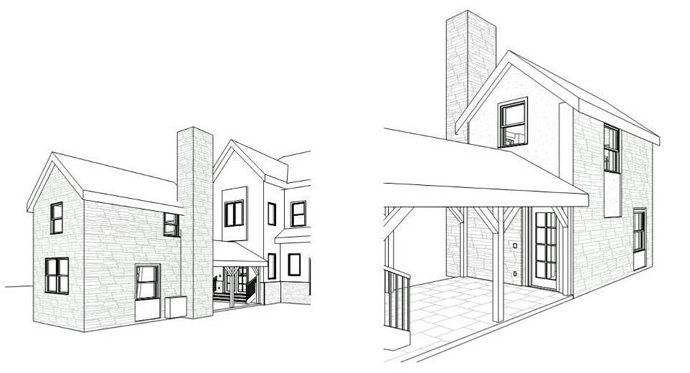
Stone house and breezeway concept views.
Construction drawings for the stone house and breezeway.
The general contractor did demolition, site preparation, and foundation work before the modules arrived. After they were set and connected (by the manufacturer’s crew), the GC did the exterior finish work and completed the interiors.
Existing house demolished, stone house exposed, and foundation poured. Ready for prefab unit delivery.The prefab units arrive on site.The modules are set into place and connected.The Client and Orion GC’s Foreman Irv Morey standing inside newly-set units. In the doorway, the joint between the units is clearly visible. Notice, also, that the unit arrived with finished trim and paint.
Last, but certainly not least, is an active, engaged homeowner. But isn’t this important for every project? We were lucky in this respect–being active and engaged seemed to come naturally to these clients.
5. What are the basic steps in the process?
- Identify a site, and determine whether modular is the right decision for either an addition or new construction,
- Select a layout to start with, customizing where necessary,
- Kickoff manufacturing / Prepare the site and foundation,
- Deliver the “boxes”,
- Complete the finishes (interior & exterior), HVAC, final plumbing, etc.,
- Move in (in our case, 3 months after box delivery).
I could go on and on about this project, but these are the basics. Contact me if you have other questions; I’m happy to talk more! In the meantime, here are some more photos:
Rear of house.Front of house just after modules were set. It took six days to set all of the modules.The finished product. From the time the modules were set (previous photo), the house took three months to complete.